Welcome to Northern Extrusion - Your trusted partner for high-quality plastic sheet
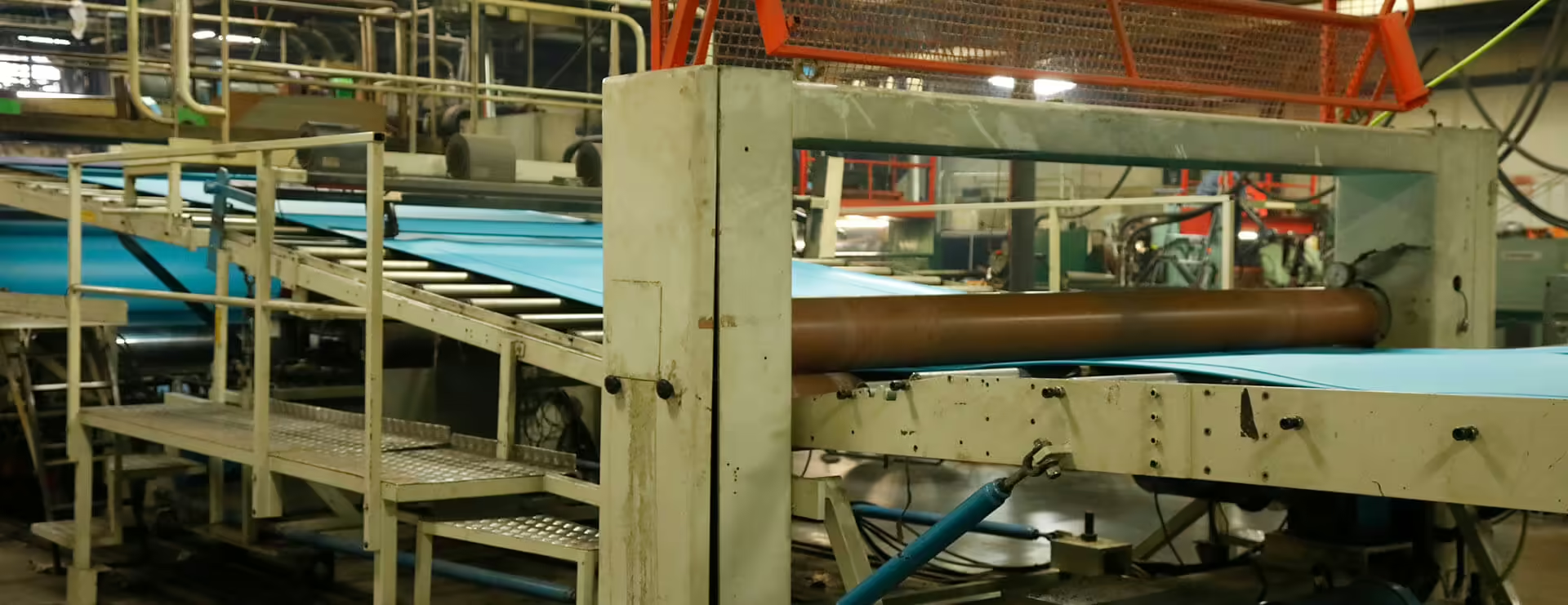
Experience the difference with Northern Extrusion
At Northern Extrusion, we are committed to sustainability and creating products that make a difference. By using recycled plastic, we are contributing to a cleaner environment while providing our clients with top-of-the-line products.
Unmatched Product Capabilities
With our state-of-the-art equipment and experienced team, we provide sheet capabilities that range from thicknesses of .060-.400, widths of 10"-100", and lengths of 2"-192". We also offer rollstock capability for even more versatility.
Our Process
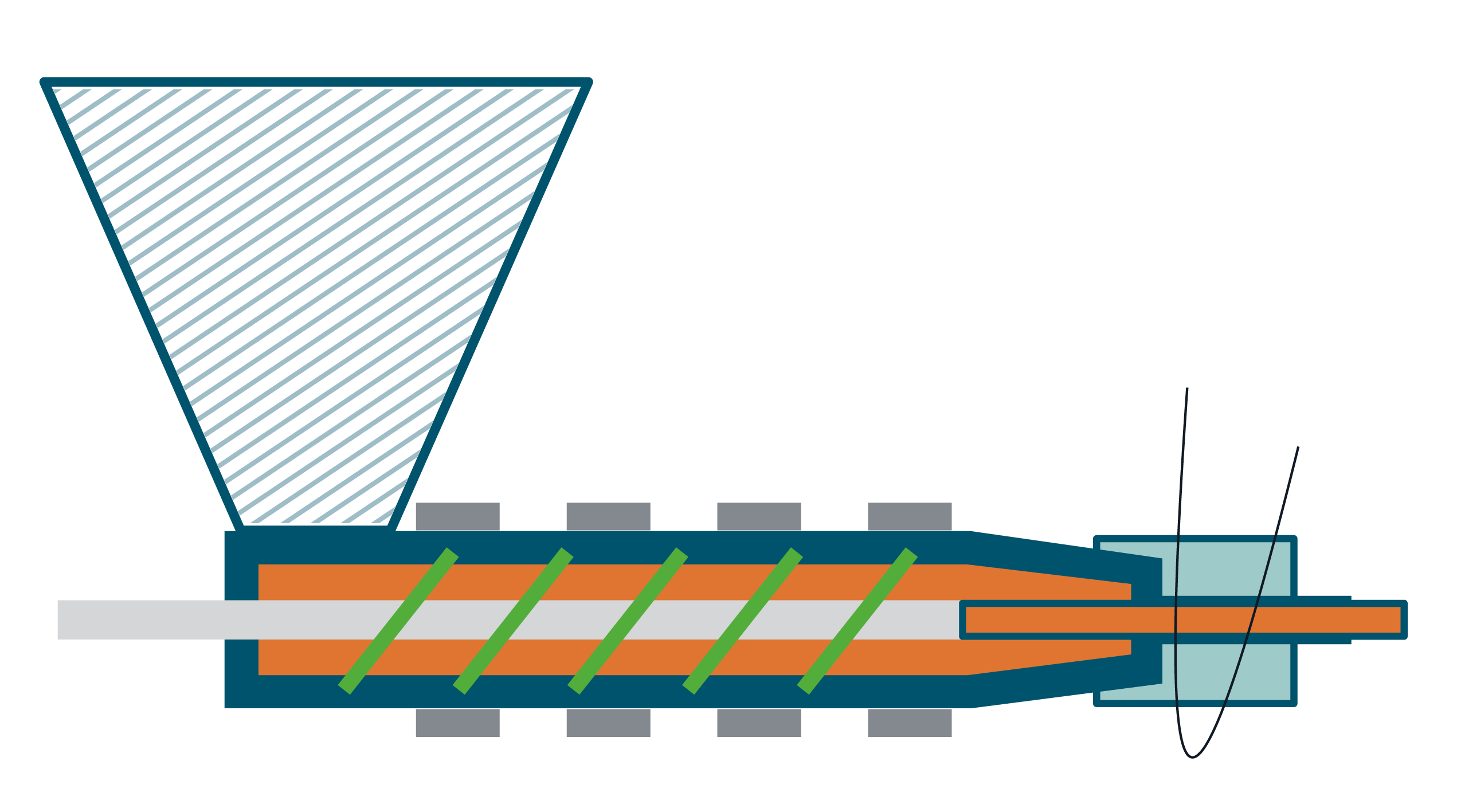
Extrusion Process
1. Material Preparation
Plastic resin, in the form of pellets or granules, is fed into a hopper. The choice of plastic depends on the desired properties of the end product (e.g., polypropylene, polyethylene, polystyrene, etc.).
2. Melting
The resin moves through a heated barrel, which consists of a long screw that rotates and drives the material forward. The combination of heat and compressive force from the rotating screw melts the plastic. The temperature along the barrel can be adjusted to ensure proper melting without degrading the material.
3. Mixing
As the plastic moves down the barrel, it is mixed thoroughly. Additives, such as colorants, stabilizers, or fillers, can be introduced at this stage to enhance the properties of the plastic.
4. Extrusion
Once the plastic is fully melted and mixed, it reaches the extrusion die, which shapes the material into a continuous profile (like sheets, films, tubes, or other shapes) as it is pushed through the die.
5. Cooling and Solidifying
After exiting the die, the extruded plastic is cooled, usually by exposure to air or water, which solidifies it into its final shape. The cooling process can affect the physical properties of the finished product.
6. Cutting/Finishing
The solidified extrudate can be cut into desired lengths or further processed depending on the application. This may include processes like trimming, surface finishing, or additional machining to meet specifications.
7. Quality Control
Throughout the process, quality control measures are typically implemented to ensure consistency in the extruded products, checking for issues like surface defects, dimensional accuracy, and material properties.
The Perfect Texture for Every Need
We understand that each product requires a unique texture. That's why we offer various textures such as smooth/smooth, haircell/smooth, fine haircell/smooth, matte/smooth, and matte/matte. You name it; we have it!
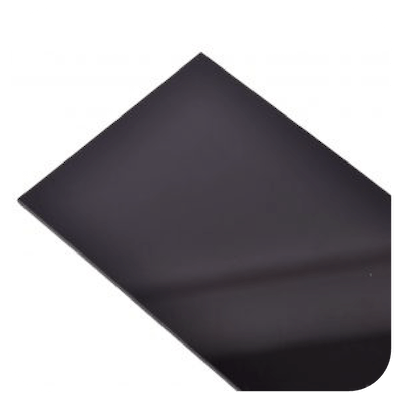
Smooth/Smooth
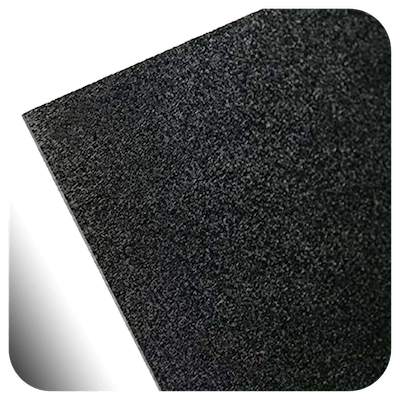
Haircell/Smooth
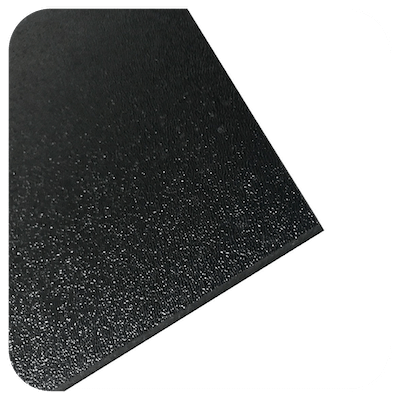
Fine Haircell/Smooth
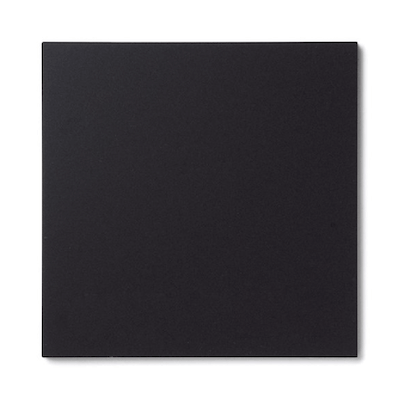
Matte/Smooth
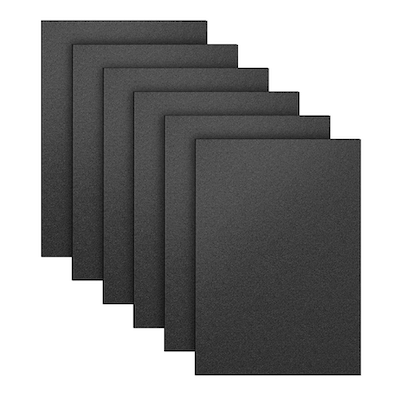
Matte/Matte
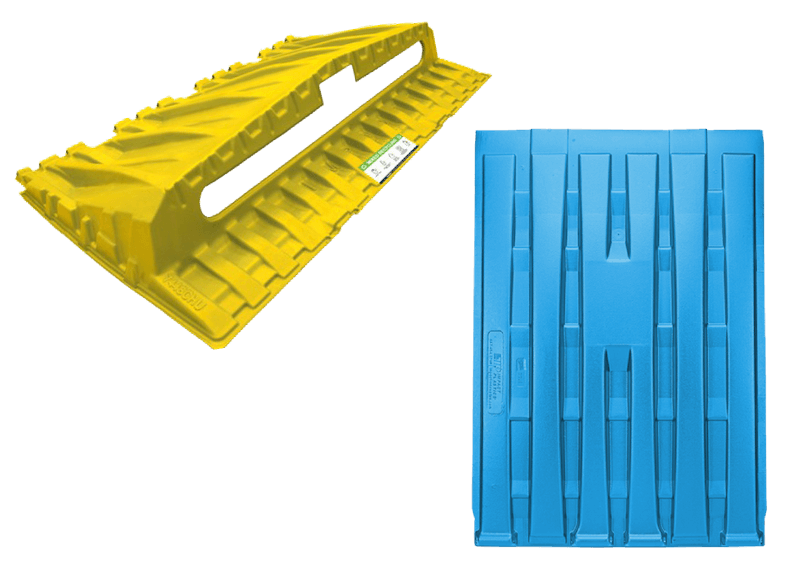
Your Partner in Customization
At Northern Extrusion, we believe in creating customized solutions that meet your specific needs. We have relationships with the best color houses in the country and can match any color under the sun. Additionally, we offer laminate overlays during the extrusion process.
Contact us today to learn more about how Northern Extrusion can help you transform your recycled plastic into high-quality products!
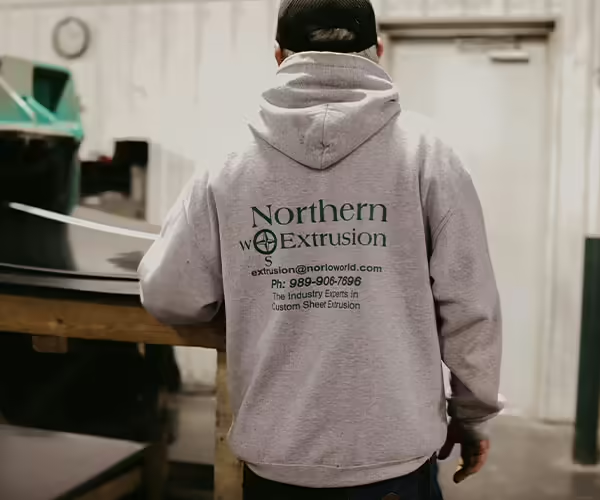